(10)
(11)
(12)
ARMY TM 9-6115-464-34
AIR FORCE TO 35C2-3-445-2
NAVY NAVFAC P-8-624-34
If adjustment does not give the proper relationship or if relationship varies outside of acceptability
limits at any point, replace load measuring unit load resistor.
Deactivate power source and remove load measuring unit from test circuit.
Install load measuring unit cover (figure 3-64).
e. Assembly.
(1) Position base (27, figure 3-84), to install diode (26), transformer (25), insulation washer (24), spacer
sleeve (23), flatwasher (22), Iockwasher (21) and screw (20).
(2) Install screw (19), insulating washer (18), load resistor (17), insulating washer, flatwasher (15),
Iockwasher (14) and nut (13).
(3) Install connector bracket (12), screw (11), flatwasher (10), lockwasher (9), and nut (8).
(4) Install connector (7), Iockwasher (6), and screws (5).
(5) Install cover (4), with flatwasher (3), Iockwasher (2) and nut (1).
f. Installation. Refer to the Operator and Unit Maintenance Manual for load measuring unit installation
instructions.
3-64. ELECTRO-HYDRAULIC GOVERNOR CONTROL UNIT.
a. General.
(1)
(2)
(3)
(4)
(5)
(6)
The electro-hydraulic governing system is a speed (frequency) sensing system used to maintain
prime mover speed constant and therefore generator output frequency, during periods of unchanging
load and when load additions or deletions occur.
The system consists of a control unit, load measuring unit and hydraulic throttle actuating unit.
The control unit inputs are the generator output voltage, and a dc voltage (O-9.8 Vdc) proportional to
the generator load, supplied by the load measuring unit. The generator voltage input is applied to a
frequency sensing network and reference voltage network. The differential output of these two
networks determines the control current of two magnetic amplifiers whose outputs drive separate
coils of the hydraulic actuators pilot valve. The actuator pilot valve positions the actuator power
piston which is connected to the input arm of the fuel injection pump. The actuators hydraulic system
is comprised of a reservoir, engine driven pump (300-320 psi, 2 gpm), cooler and filter.
Any deviation of engine speed, reflected as a change in frequency at the input of the governor,
produces a change in the magnitude and direction of magnetic amplifier control field current. This
change in control field current will increase the strength of one coil of the pilot valve while decreasing
the strength of the other. The resultant difference repositions the pilot valve in turn repositioning the
power piston which changes the output of the fuel injection pump, changing engine speed and
consequently restoring generator frequency to its nominal value.
The load measuring units (LMU) input to the governor control provides for automatic load sharing
when two or more sets are operated in parallel. Each set is equipped with an LMU.
If the load added to the system is not equally divided, the LMU inputs to their respective governors
will differ. The resulting difference acting through additional windings of each sets governor (which
are connected in parallel) will reposition each sets actuator power piston such that fuel flow in the
more lightly loaded set is increased. Since the power input of each prime mover has been
readjusted, equal division of true power (Kw) occurs with no deviation in frequency of any set.
b. MaIfunction. The following procedures are to be performed in the generator set unless otherwise
specified.
3-157
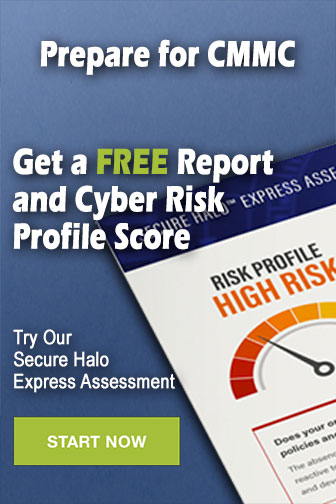